Maintenance software to organize your maintenance work, inspection, repair, material management and outsourcing.
Free trial of maintenance software: download here
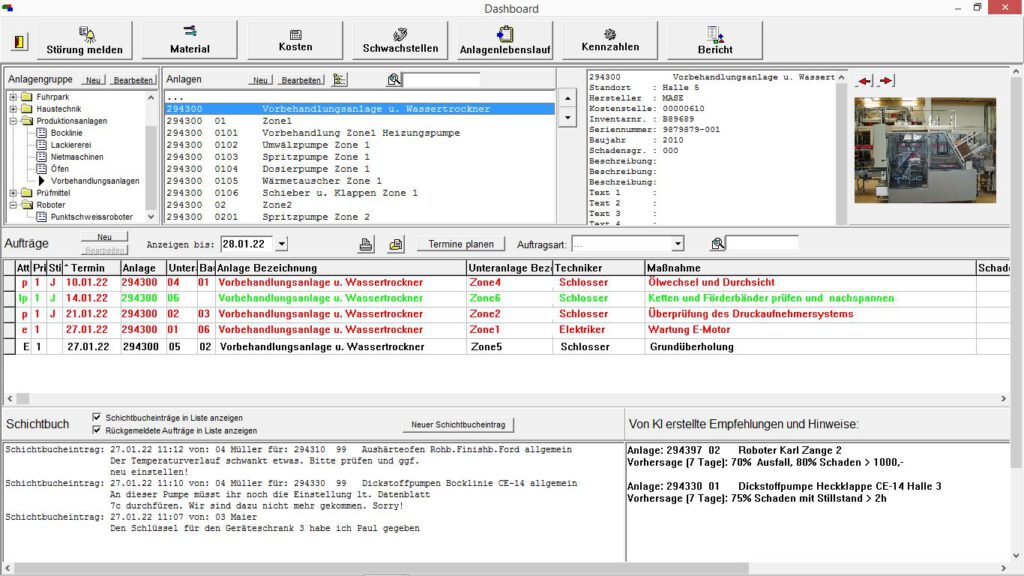
Maintenance software: Dashbord
Dashbord: Equipmentgroups, equipment, workorders, scheduling,
workorder queue, shiftworker notes, recommendation by AI, reports,
material, data history, equipment lifecycle, etc
The maintenance software EXPERT-maintenance enables
planning, control and analysis of maintenance, inspection, repair work,
material planning and external-company management.
If your company is certified according to DIN ISO 9000, you can benefit from
valuable support through special functions of the software.
Maintenance software: Work orders and scheduling
This types of workorders are possible:
– Periodic maintenance order with an interval based on time,
– Periodic maintenance order with operating data interval,
– Individual repair order,
– Unplanned repair order
– Fault logging.
Data input in user friendly entry fields is very easy:
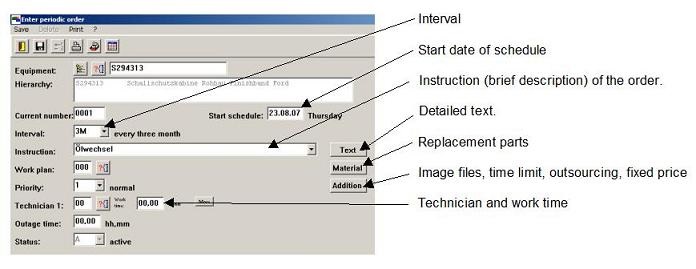
Equipments, assemblies or subassablies can be structured in a hierarchy.
The system structure existing in your company can be adopted.
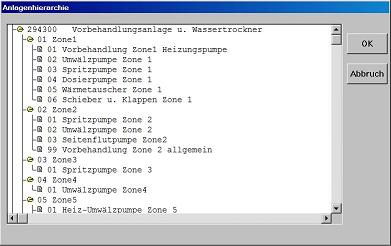
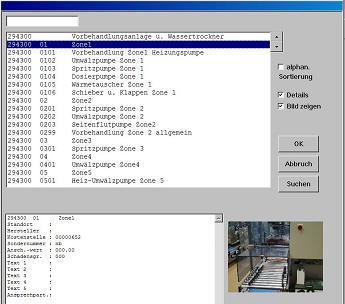
Maintenance software: Dashboard / Work order queue
The Work order queue is a frequent function for the technicians. All orders
due and logged faults are displayed.
Work papers and material notes and also image files can be printed or send
as an email from this queue with all data required for carrying out the work.
Collective work papers for routine work can be printed instead of the detailed
work papers. Email functions are available.
The orders must be acknowledged after processing. At the same time, all
changes to the data specified in the work paper are entered.
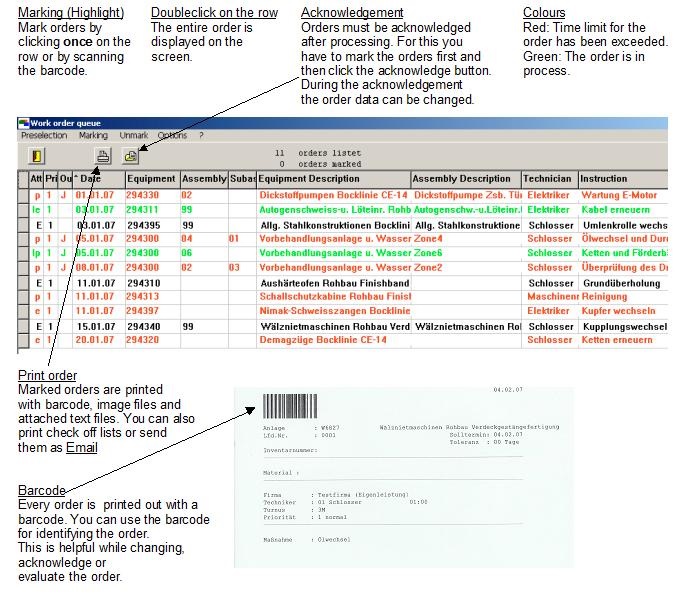
Barcodes
All maintenance, inspection and repair orders are automatically printed with
a barcode for faster identification and acknowledgement. It is also quicker
to log faults via barcode checklists.
Mobile barcodescanner or smartphone apps can be used.
Drawings and photos
You can assign drawings or photos to your equipment, work orders or spare parts.
They are printed out for each work schedule to illustrate the orders .
Maintenance software: Data history
The data history is a requirement for preventative maintenance. This makes it
possible to target weak points and recognize wear tendencies. All completed and
reported work orders are saved in a special history file for the following evaluations.
Equipment or machine life cycles
All maintenance work from procurement onwards is listed with system downtimes
and costs. In conjunction with the order archive you will receive an exact list of
all work to the Equipment or machine.
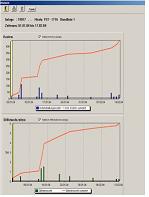
Weak point analysis
The frequency of damage to a system is shown graphically. Weak points can
immediately be seen and system improvements can be evaluated.
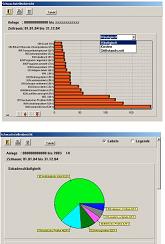
Schedule overview graphics
You are provided with graphics showing a clear overview of all work schedules
for the selected time period.
Personnel capacity planning
You can effectively avoid overtime or insufficient capacity utilization by your
personnel on the basis of graphics and evaluation lists.
System availability overview / Downtime planning
A special list shows you the system downtimes due to maintenance measures.
It is especially suitable for coordination with production.
Cost accounting
To promote cost transparency, you can gain an overview of the costs to be
expected for the planned maintenance for the selected time period. You can
also compile exact cost lists for completed maintenance work.
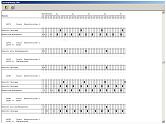
A special list shows you the system downtimes due to maintenance measures.
It is especially suitable for coordination with production.

Budget control
Here you can receive information on the budget consumption divided into
in-house, external and material costs as well as on further development of the
consumption based on a cost prognosis.
Maintenance software: Material management / Warehousing
Spare parts, consumable materials and tools for the maintenance work are
managed with the material planning and management.
Parts lists
In the event of a fault, you can immediately get an idea of which spare parts are
needed, etc. In this way, you can effectively shorten system downtimes.
Material tracking
You can obtain information concerning which systems or system parts certain
spare parts are installed in.
Purchase lists
You are prompted to purchase spare parts at an early date, with consideration
of the delivery time, if their reserves need to be replenished. Material
bottlenecks are therefore avoided and system downtimes shortened, as the
right spare parts are always in stock.
Cost monitoring and cost-relevant allocation
Handling frequency monitoring. Just-in-time support
Shift worker notes
A digital shift worker notebook is integrated in the software EXPERT-maintenance.
Easy and save changing of shifts is supported by showing:
– shift worker notes
– maintenance work to do
– maintenance work that has been done by the previous shift team
– photos for documentation
Just-in-time support
Outsourcing management
An implementation by external companies can be more cost effective for
certain maintenance work. The system provides you with support for this in
the following ways:
Tender documents are printed.
The implementation of maintenance work is controlled via daily, weekly or
monthly order sheets.
The work carried out is monitored via acceptance records.
The compiled invoice is checked via an invoice control sheet.
Cost comparisons between external companies and between external
companies and in-house service can be realized via selected orders.
External companies and in-house services can be managed simultaneously.
Key indicators for maintenance
Indicators like MTBR (mean time between repair) and MTTR (mean time to repair)
can be listed.
Interfaces to other software
The software EXPERT maintenance has a flexible interface for production planning systems and is especially suitable as a cost-effective and user-friendly substitute for maintenance modules of these systems. In addition, interfaces to all current databases or application programs are possible.
Maintenance software: System adaptation to your company
The entire maintenance software EXPERT-maintenance has a modular structure.
We compile a system precisely tailored to your company from our complete
program for your special requirements. In addition, each individual module can be
arranged so flexibly that you yourself do not have to adapt to the system, but
instead the system adjusts to you.
____________________________________________
Maintenance software: App for smartphones and tablets
With our app for smartphone and tablets you can:
Report faults with the app (Fault logging)
With description, photos, barcodes, etc
The reported faults are immediately appearing in the
work order queue of the windowssoftware
EXPERT maintenance.
Receive equipment-Infos
Get all due orders of a selected
equipment and show them on the display. In addition
you can get the order-history.
Carry out workorders
show the order data on the display,
input comments on the workorder,
make photos, acknowledge the workorder after processing.
Shift worker notes
Read the shift worker notes and add text.
____________________________________________
Maintenance software: Fault logging and Ticketingsystem
The maintenance software EXPERT-maintenance contains a
special mask for logging fault messages (ticketingsystem).
This mask is licence-free and can be installed in the
company as often as you like.
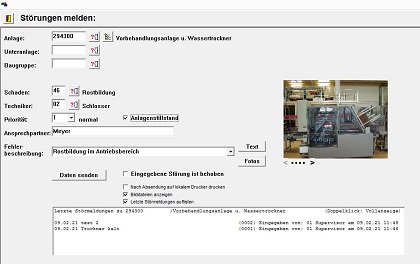
This mask is used to log faults which then appear as open
faults in the work order queue of the EXPERT-maintenance.
They are processed and acknowledged there.
After this they are saved in the history for evaluation.
Entry of the fault can be simplified by using barcodes so
that no more data has to be entered via the keyboard but
instead the fault is scanned in using barcode lists.
Our app for smartphones and tablets can also be
used for reporting faults.
____________________________________________
Digital shift worker notebook
A digital shift worker notebook is integrated in the software
EXPERT-maintenance.
Easy and save changing of shifts is supported by showing:
– shift worker notes
– maintenance work to do
– maintenance work that has been done by the previous shift team
– photos for documentation
You can also use the mobile app to read the shift worker notes and
add text.
____________________________________________
Barcodes and QRCodes
In the maintenance software EXPERT-maintenance, barcodes are
automatically printed out on all orders, order lists, removal lists,
catalogues etc. The barcodes are printed out on normal printers.
No special barcode printer is necessary.
The barcodes e.g. are for rapid acknowledge of orders, changing
orders, removing material etc.
There is no need for a complicated and time-consuming entry
of numbers or letters.
Fault logging:
The fault logging can be simplified by the use of barcode lists
so that no data has to be entered via the keyboard. Faults are
logged by scanning in barcode lists (which are compiled in the
catalogues module).
Our app for smartphones and tablets can also be used for
reporting faults.
Mobile barcode scanner:
Mobile barcode scanners can be used to process and finalize orders,
while logging faults. After processing the orders or faults are
transferred to the EXPERT-maintenance as normal orders.
Further information on the use of mobile barcode scanning in
conjunction with the maintenance software EXPERT-maintenance
is available on request.
____________________________________________
Modules of the software
The software EXPERT-maintenance is divided into a basic module
and several additional modules. Only the basic module is absolutely
essential for use of the EXPERT-maintenance. The additional modules
can be selected as and when required and purchased later if need be.
Basic module:
Work orders, queue, scheduling, master data, etc
Additional modules:
Schedule overviews
Personnel management
Equipment downtime planning
Cost accounting
Material management
Data history including:
– Equipment life cycle
– Weak point analysis
Outsoucing management
Catalogues
Shift report
Key indicators for maintenance (MTBR, MTTR)
____________________________________________
Frequently asked questions (FAQ)
Below you can find answers to the questions most frequently
asked by users of this website. If you cannot find an answer to
your question on this page, please send us an email: info@ibrue.de
The maintenance software EXPERT-maintenance is
too extensive for our needs. Can we purchase parts
of the software? Yes. The maintenance software EXPERT-
maintenance has a modular structure. You can select the modules
suitable for you from the complete scope of the modules.
Modules not purchased can be upgraded at any time.
Is training necessary for operating the maintenance
software EXPERT-maintenance? No. The maintenance
software EXPERT-maintenance is so user-friendly that no
training is necessary!
Is the maintenance software EXPERT-maintenance
network-compatible? Yes. Five network licences are included
in the price. Maximum 99 users are possible.
Can the maintenance software EXPERT-maintenance
only be used for certain industrial sectors? The maintenance
software EXPERT-maintenance can be used across sectors.
Are there special hardware requirements? No. The
software runs under WINDOWS 7, 8 or 10
Do database licences have to be purchased
for operating the maintenance software EXPERT-
maintenance? No.
How can fault messages be entered and edited in
the maintenance software EXPERT-maintenance?
Faults can be reported via the fault message mask. The fault
message mask is licence-free and can be installed as often as
you like in the company.
Does the maintenance software EXPERT-maintenance
support Internet functions? Yes. For example, work
orders can be sent as email. Material orders can be sent by
email directly from the material management. If using the
maintenance software EXPERT-maintenance in several plants
at different locations, spare part search enquiries can typically
be sent from one plant to the other etc.
Does the maintenance software EXPERT-maintenance
support Microsoft standard software? Yes. You can attach
Word or Excel files to a work order of the maintenance software
EXPERT-maintenance for example. All results of evaluations of
the maintenance software EXPERT-maintenance can be transferred
directly to an Excel table.
Does the maintenance software EXPERT-maintenance
support photos and drawings? Yes. All image formats are
supported. You can typically record image files for system master
data, material master data and work orders.
Can data be incorporated in the maintenance software
EXPERT-maintenance from already existing databases
or old application programs? Mostly yes.
Are interfaces to other programs (especially to production
planning programs) possible? Yes.
Is the software EXPERT-maintenance available in other
languages than German or English ? Yes. Polish, Hungarian,
Romanian, Turkish, Italian, Spanish, French, Lithuanian, Latvian,
Russian, Dutch and Portuguese
____________________________________________
EXPERT maintenance is the English version of the German
software EXP-Instandhaltung
____________________________________________
Free trial software: download here
____________________________________________